Space electronics hardware faces unique challenges, from extreme vibrations during launch to varying thermal conditions in orbit. This article will provide an in-depth look at the development and significance of space electronics hardware, focusing on the J-STD-001 standard and its addendum tailored for space applications. We will discuss the requirements of these standards set to ensure electronic assemblies' reliability in space environments. Furthermore, we will highlight EPTAC's role in offering training and certification, ensuring professionals are equipped with the necessary knowledge to meet these stringent standards.
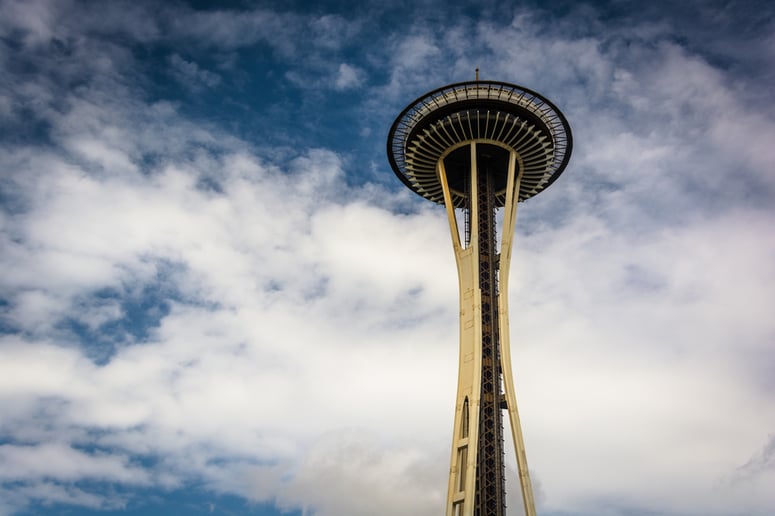
The Evolution of Space Electronics Hardware
Space exploration, with its inherent challenges, has always necessitated advancements in electronics hardware. The journey began with the development of large and relatively efficient rockets during the mid-twentieth century. The world's first large-scale experimental rocket program, Opel-RAK, led by Fritz von Opel and Max Valier in the late 1920s, laid the foundation for subsequent space missions. This program introduced the first crewed rocket cars and rocket planes, setting the stage for the V2 program during the Nazi era and subsequent US and Soviet space activities from the 1950s onwards.
The real turning point in space electronics came with the launch of the Soviet Union's Sputnik 1 on October 4, 1957. This satellite, the first human-made object to orbit Earth, weighed approximately 83 kg and orbited at a height of about 250 km. Equipped with two radio transmitters, it provided invaluable data on the electron density of the ionosphere. This marked the beginning of a series of milestones achieved by the Soviet space program, including the first human in space, Yuri Gagarin, aboard Vostok 1 in 1961, and the first spacewalk by Alexei Leonov in 1965.
However, as space missions evolved and aimed for more distant celestial bodies, the electronics hardware had to keep pace. The first artificial object to reach another celestial body was Luna 2, which reached the Moon in 1959. This was followed by Luna 9, which achieved the first soft landing on the Moon in 1966. As missions became more complex, the demands on electronic assemblies grew exponentially. They had to function reliably in space's harsh environment, from the intense radiation to the extreme temperatures.
The early era of space exploration was characterized by competition, primarily between the Soviet Union and the United States. This competition drove rapid advancements in technology and led to a deeper understanding of the requirements for reliable space electronics hardware. As the focus shifted from competition to cooperation in subsequent years, with projects like the International Space Station (ISS), a joint venture between Russia, the United States, Canada, and several other countries, the emphasis on reliable and robust electronics hardware became even more pronounced.
In the contemporary era, especially in the US, there has been a significant emphasis on reusable spacecraft. Companies like SpaceX and Blue Origin have been at the forefront of developing technology for orbital launches. SpaceX's Dragon 2, for instance, is a testament to the advancements in space electronics hardware, designed to be both crewed and uncrewed, showcasing the flexibility and robustness of modern space electronics.
Classification and Functions of Space Electronics Hardware
Space electronics hardware is integral to spacecraft operation, addressing challenges such as radiation, temperature extremes, and microgravity. These components are engineered for the specific demands of space environments. Here's an overview of the primary types of space electronics hardware:
- Communications Systems: Essential for data transmission between the spacecraft and terrestrial stations. Communications satellites relay and amplify telecommunication signals, facilitating data exchange between different terrestrial locations.
- Navigation Systems: These systems provide trajectory control and spacecraft positioning. They utilize onboard computational units, sensors, and algorithms to determine and adjust the spacecraft's course.
- Power Systems: These systems supply energy to the spacecraft. Components include solar arrays for energy capture, energy storage batteries, and power distribution mechanisms.
- Life Support Systems (for crewed missions): Vital for maintaining suitable conditions for astronauts. They manage oxygen supply, carbon dioxide removal, waste processing, and ensure appropriate temperature and pressure levels.
- Scientific Instruments: Spacecraft equipped for research purposes carry instruments like telescopes, spectrometers, and imaging devices.
- Propulsion Systems: These mechanisms enable spacecraft movement and trajectory adjustments. They encompass thrusters, engines, and other thrust-producing devices.
- Structural Components: These elements constitute the spacecraft's physical framework, safeguarding internal components and ensuring structural stability.
- Onboard Computers and Control Systems: Central to spacecraft operation, these systems process sensor inputs, execute commands, and manage other systems.
- Thermal Control Systems: Due to the vast temperature fluctuations in space, these systems maintain operational temperature ranges using components like radiators, insulators, and thermal regulators.
- Cargo Systems: For missions transporting materials, such as resupply tasks to space stations, these systems incorporate storage units, docking mechanisms, and material transfer apparatuses.
Recognizing the distinct types of space electronics hardware and their operational roles is crucial for professionals in spacecraft design, production, or management. Each component's reliability and performance are paramount for mission success.
J-STD-001 and J-STD-001 Space Electronics Hardware Addendum
Spacecraft operations rely heavily on a diverse array of electronics hardware, from communication systems to thermal control units. Each component, be it the onboard computers responsible for data processing or the propulsion systems for trajectory adjustments, plays a specific role in spacecraft functionality. Given the challenges these components face in space environments, there's a clear requirement for rigorous standards to ensure their reliability. This is where the J-STD-001 standard comes into play. Developed as a comprehensive guideline for soldered electrical and electronic assemblies, it sets precise criteria to ensure the reliability of each hardware unit within a spacecraft. This section will focus on the technical aspects of the J-STD-001 standard and its dedicated addendum for space electronics, highlighting their significance in spacecraft design and operation.
The J-STD-001 standard, officially titled "Requirements for Soldered Electrical and Electronic Assemblies," is a globally recognized guideline that sets the bar for soldering processes and materials. Developed by the IPC (Association Connecting Electronics Industries), this standard has become the industry's benchmark for ensuring the reliability of soldered electrical and electronic assemblies.
The significance of J-STD-001 lies in its comprehensive approach. It addresses everything from material requirements to the methods and verification criteria for producing high-quality soldered interconnections. The standard emphasizes the importance of process control, providing manufacturers with a clear roadmap to achieve consistent and reliable soldered connections.
However, space-bound electronics face unique challenges, from extreme vibrations during launch to the thermal cyclic environments of space. Recognizing these challenges, the IPC introduced the J-STD-001 Space Electronics Hardware Addendum. This addendum emphasizes rigorous standards to ensure the reliability of soldered electrical and electronic assemblies in space environments. It addresses various aspects, including inspection criteria, material specifications, and process control enhancements. However, a significant component is personnel proficiency.
The addendum stipulates that all personnel, including instructors, operators, and inspection staff, must exhibit proficiency in their tasks. Objective evidence of this proficiency is required, which can include:
- Training records relevant to specific job functions.
- Documented work experience.
- Tests conducted based on this standard's requirements.
- Periodic reviews assessing an individual's proficiency.
Training protocols in the addendum align with the IPC J-STD-001 Training and Certification Program, with emphasis on the Space Requirements for Soldered Electronic Assemblies. For operators, training covers Module 1, Modules 2 through 6 (as applicable), and the Space Addendum.
All training must be traceable to an IPC Master Instructor, ensuring adherence to IPC standards. Additionally, each training session, examination, and proficiency demonstration should be overseen by an IPC Master or Registered Instructor.
The addendum also specifies the training environment, highlighting the need for structured training in a classroom setting. On-the-job training, even under supervision, is not considered adequate for space hardware fabrication as per the addendum's guidelines.
EPTAC's Role in Elevating Space Electronics Expertise
Building on our exploration of the J-STD-001 Space Electronics Hardware Addendum and the importance of personnel proficiency, it is crucial to highlight the role of specialized training and certification programs in ensuring that professionals are adequately equipped to meet these standards. EPTAC, a recognized leader in solder training and IPC certification, offers specific modules tailored for aerospace and space electronics professionals, ensuring they are well-prepared to handle the unique challenges of space electronics:
J-STD-001 Aerospace Instructor
EPTAC offers a J-STD-001 Aerospace Instructor program that delves into the J-STD-001 Space Electronics Hardware Addendum. This addendum provides additional requirements over the IPC J-STD-001 to ensure the reliability of soldered electrical and electronic assemblies in space environments. The 1-day program consists of a lecture reviewing each section of the addendum, followed by an open book exam. This module is an optional addition to the J-STD-001 Instructor Training Program.
J-STD-001 Aerospace Specialist
The J-STD-001 Aerospace Specialist program is another offering by EPTAC. This 1-day program focuses on the J-STD-001 Space Electronics Hardware Addendum, ensuring specialists are well-versed in the additional requirements for space electronics. The program concludes with a 25-question open book exam.
J-STD-001 Aero Instructor (Recert)
For those who have previously undergone the Aerospace Instructor training, EPTAC offers a recertification program. This ensures that instructors remain updated with the latest requirements and standards. Recertification is due every 24 months.
J-STD-001 Aero Specialist (Recert)
Similarly, specialists can undergo a recertification program to ensure they remain current with the evolving standards of the J-STD Space Addendum. This recertification is also due every 24 months.
EPTAC's commitment to providing top-tier training and certification programs for space electronics professionals underscores the importance of specialized knowledge in this field. By ensuring that professionals are equipped with the latest standards and practices, EPTAC plays a pivotal role in advancing the reliability and success of space electronics.
About EPTAC
EPTAC is an internationally recognized leader in solder training and IPC certification, providing professionals with the skills to accelerate their careers, and businesses, the talent to succeed. For over 35 years, EPTAC has been helping corporations increase quality standards, improve productivity, and maximize profits. With 24 locations in North America, EPTAC continues to expand its offerings and exceptional instructional staff to provide easy access to knowledge and skill-based programs when and where the industry demands it. Access our scheduled programs through our website or schedule your own corporate on-site training. For information, call 800.643.7822 or contact us.