Leaded solder has been the preferred material for electronic manufacturing for decades due to its low cost, lower melting point, and ease of use. However, there has been heightened concerns about the health and environmental effects of lead solder, particularly when used in electronics.
In 2006, the European Union banned certain hazardous substances in electronic products, including lead.
In the past two decades, the electronic manufacturing world has experienced a dynamic development of alternative soldering material centered on tin metal, with manufacturers switching to lead-free solder alternatives in order to eradicate lead from electronic production.
But what’s the right choice? Which is better for electronics manufacturing: lead-based solder or lead-free-solder?
What are Lead and Lead-Free Solders Made Of?
Leaded solder is a metal alloy that’s composed of lead and tin as its base components. It is also known as SNPB solder. Lead pipes and any water supply pipes that are joined with lead solder were banned a long time ago in new US plumbing systems to help with the restriction of hazardous substances. Lead alloys have a melting point of 183°C.
The advantages of using leaded solder include:
- It’s easier to bring to working temperature
- It’s shock resistant
- There are fewer internal flaws in the structure after cooled
However, it’s important to note that lead material is harmful to the body as it’s readily absorbed.
Lead-free solders typically contain a variety of different metals. Some of the components you may find in lead-free solder include tin, copper, silver, nickel and zinc. The most common lead-free mix is tin-copper, which has a melting point of 217°C.
The higher melting point makes lead-free solder more challenging to work with. The main reason why manufacturers are shifting to the use of lead-free solder is to eradicate lead from electronic production and waste recycling processes.
Comparing Costs of Lead-Free vs. Leaded Solder
Leaded solder is more cost-effective than lead-free solders because lead is much cheaper than alternative alloys. Lead is barely one-tenth the price of tin, making leaded solder easily affordable. Furthermore, some manufacturers replace tin with silver as their lead alternative in lead-free solders, making them even more expensive.
Lead-free solder typically costs more than leaded solder due to the additional materials and processing required to produce it. In addition to the initial cost of the solder, there may be additional costs associated with using lead-free solder. The higher melting temperatures can cause increased wear and tear on equipment, as well as higher energy costs.
However, you may also run into added costs using leaded solder. Since it can pose a health risk to those who work with it, you may end up with increased costs for safety equipment, monitoring, and disposal of hazardous waste.
Environmental Concerns of Leaded Soldering
Companies that value environmental conservation state that the main reason for embracing lead-free soldering is because of the poisonous nature of lead. The use of leaded soldering can result in contamination of the air, water, and soil during the manufacturing process, and disposal of leaded soldering waste can also contribute to environmental pollution.
When leaded solder is used in electronic products, it can also pose a risk of environmental contamination when the products are discarded after the consumer is finished with them. Once in the environment, lead can bioaccumulate in the food chain, just like all metals.
Why is Leaded Solder Bad For You?
Lead exposure poses numerous health risks, which is why lead free solder is a safer alternative. Here's why leaded solder is bad for you:
- Skin: Direct skin contact, especially with open wounds, can lead to lead absorption.
- Inhalation: Fumes released during soldering, particularly when solder reaches its melting point, can be inhaled through the nose or mouth.
- Ingestion: Lead particles can be ingested if hands are not thoroughly washed after handling leaded solder.
- Neurotoxicity: Lead's neurotoxic effects can result in damage to the nervous system and brain, leading to concentration issues and cognitive impairments.
- Kidney Damage: It can cause significant harm to the kidneys, increasing the risk of kidney disease.
- Developmental Issues in Children: Children are particularly vulnerable to lead exposure, which can lead to developmental delays and behavioral problems, even at low exposure levels.
Although traditional leaded solder contains amounts of lead considered too low for severe immediate health issues, the risk of exposure is still present, especially when solder reaches its melting point. Lead free solder offers a safer alternative, significantly reducing these health risks.
Which Solder is Better: Lead or Lead-Free Solder?
Leaded solder is easier to use, has a lower melting point, is low cost, and causes fewer quality problems with the solder joints than lead-free solder, however; the continued efforts to take lead out of all electronic products in the United States means that leaded solder could be obsolete in the next 10 years in numerous commercial applications.
Generally, it is more economical and effective to use lead solder because of its unique properties and benefits. There continue to be some industries that use leaded solders because of these properties and benefits.
The primary reason you should opt for lead-free solders, if you are able to, is if your government prohibits lead from being used in products or if you are working to be an Environmental, Social, and Corporate Governance (ESG) company.
All sectors that use solder in large quantities are likely to shift to lead-free soldering soon if they have not done so yet. The paint and gasoline sectors have both gone lead-free. As manufacturers begin to shift away from leaded solder, make sure you are up to date on your training and learn more about lead-free solder and leaded soldering from industry experts with EPTAC.
With high-level soldering courses, you can get hands-on experience from instructors who know the industry inside and out—further your soldering education with online training courses from EPTAC.
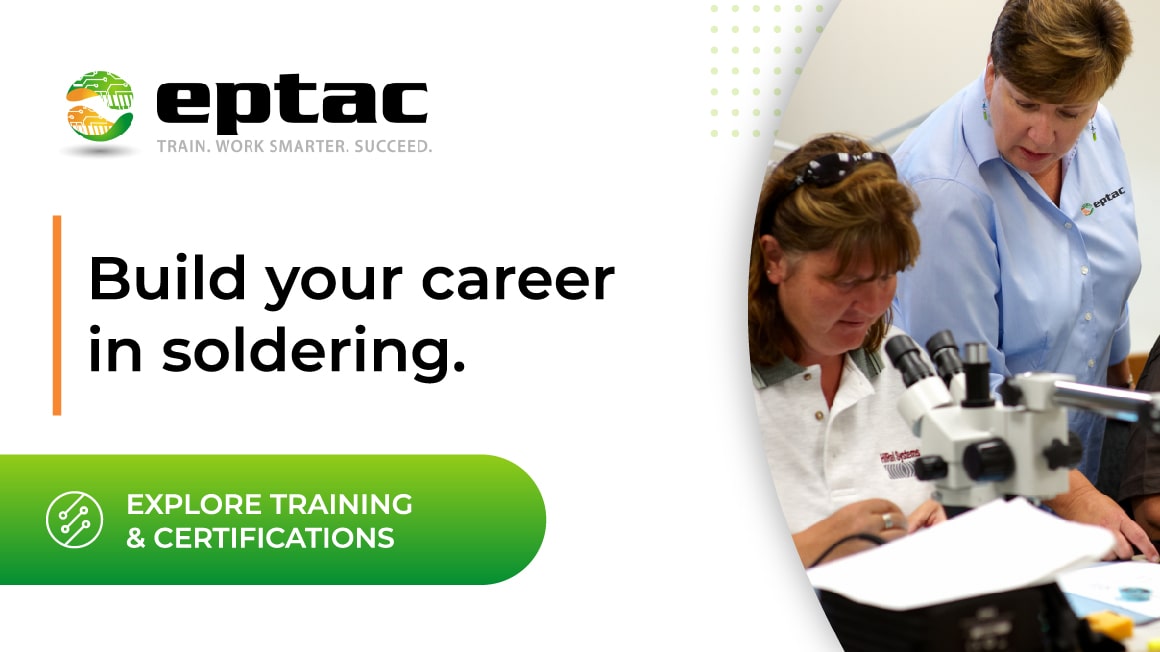
About EPTAC
EPTAC is an internationally recognized leader in solder training and IPC certification, providing professionals with the skills to accelerate their careers, and businesses, the talent to succeed. For over 35 years, EPTAC has been helping corporations increase quality standards, improve productivity, and maximize profits.
With 24 locations in North America, EPTAC continues to expand its offerings and exceptional instructional staff to provide easy access to knowledge and skill-based programs when and where the industry demands it.
Access our scheduled programs through our website or schedule your own corporate on-site training. For more information, call 800.643.7822 or contact us.