Standards in electronics manufacturing, particularly in the PCB manufacturing process and PCB assembly, form the foundation for product design, development, and deployment. These standards establish guidelines, best practices, and technical specifications, ensuring products meet critical quality and reliability criteria.
This is vital in an industry where precision is key, and the consequences of a defective product can be significant, highlighting the importance of adhering to these standards in every aspect of the creation and assembly of printed circuit boards.
Standards in electronics making are important for three main reasons. First, they help make sure products are of good quality and last a long time. For example, following standards can reduce mistakes in making products by a lot.
Second, standards make sure electronic components are safe, especially when they are used in important areas like hospitals, transport, and defense. Lastly, standards help different electronic products work well together, so there's no trouble when using devices from different companies together.
In this blog article, we'll explore the various electronics manufacturing standards, with a special focus on IPC standards and how they compare to others. We'll also delve into how EPTAC plays a pivotal role in helping professionals understand and implement IPC standards effectively.
Join us as we navigate the world of electronics standards and the unique offerings of EPTAC.
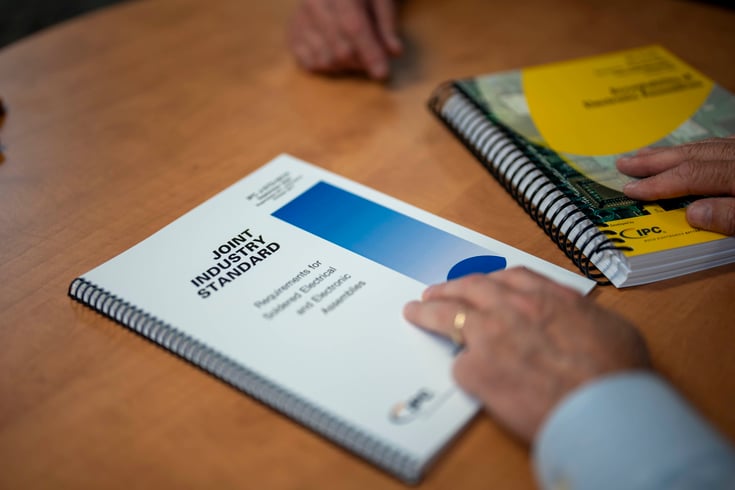
Common Electronics Manufacturing Standards
These standards, developed by various international bodies, provide guidelines that manufacturers adhere to, ensuring that electronic products meet specific criteria. Below is a table detailing some of the most prominent electronics manufacturing standards:
Standard
|
Coverage/Scope
|
IEC
|
The International Electrotechnical Commission (IEC) develops international standards for electronics and electrical technologies. These standards, derived from global consensus, guide the design, manufacture, and testing of electronic devices and systems. Notably, close to 80% of European electrical and electronic standards are IEC International Standards, underscoring their widespread adoption and significance.
|
IEEE
|
The IEEE Standards Association (IEEE SA) is a key division of the IEEE, dedicated to developing global standards for various industries, including electronics manufacturing. With a rich history, the IEEE SA emphasizes balance, openness, and consensus in its standards creation. Notably, they have over 1,200 active standards, with 650+ in development, highlighting their commitment to quality and innovation in electronics.
|
ANSI
|
The American National Standards Institute (ANSI) oversees the development of voluntary consensus standards in the U.S., including those pertinent to electronics manufacturing. By ensuring consistent product characteristics and performance, ANSI promotes interoperability and safety in electronic products. The organization harmonizes U.S. standards with international ones, facilitating global acceptance of American electronic goods. ANSI's role is pivotal in setting benchmarks that allow products from different manufacturers to integrate seamlessly.
|
JEDEC
|
The JEDEC memory standards, established by the Joint Electron Device Engineering Council (JEDEC) Solid State Technology Association, provide specifications for semiconductor memory circuits and storage devices. JEDEC's aim is to clarify interactions between manufacturers and purchasers, ensuring product compatibility and aiding in efficient product selection.
|
RoHS
|
The Restriction of Hazardous Substances Directive (RoHS) is a European Union initiative that limits hazardous chemicals in electronics. Effective from 2006, it restricts ten harmful materials in electronic and electrical equipment, aiming to make products safer for consumers and the environment. This directive works alongside the Waste Electrical and Electronic Equipment Directive (WEEE) to promote recycling and reduce toxic substances like lead, mercury, and certain flame retardants in electronics.
|
ISO
|
The International Organization for Standardization (ISO) provides globally recognized standards across various sectors, including electronics manufacturing. These standards, like the ISO 9000 family for quality management and ISO/IEC 27001:2022 for information security, ensure products meet high-quality, safety, and efficiency benchmarks. By following ISO standards, electronics manufacturers align with international best practices and quality expectations.
|
NEMA
|
NEMA publishes more than 1,000 electrical and medical imaging standards and technical documents based on the latest science and engineering. NEMA standards promote the safety, efficiency, resilience, and sustainability of products and systems used to power the world.
|
ETSI
|
The European Telecommunications Standards Institute (ETSI) is a non-profit organization that standardizes information and communication technologies. Recognized by the European Union, ETSI develops technical standards for systems like GSM™, TETRA, and 5G. Collaborating with other standardization bodies, ETSI ensures interoperability and smooth integration of various technologies, especially in areas like Wireless Systems and Public Safety.
|
ITU
|
The International Telecommunication Union Telecommunication Standardization Sector (ITU-T) is a crucial division of the International Telecommunication Union (ITU). It formulates standards vital for telecommunications and Information Communication Technology (ICT), impacting electronics manufacturing. Noteworthy standards include X.509 for cybersecurity and H.264/MPEG-4 AVC for video compression. Developed in collaboration with global members, these "Recommendations" by ITU-T ensure consistent quality and interoperability in electronics manufacturing.
|
SAE
|
SAE International, originally focused on automotive engineering, has expanded its standards development to encompass various transport sectors, including aerospace and commercial vehicles. While its roots are in vehicle design and safety, SAE has evolved to address the growing complexities of electronics manufacturing within transportation. By establishing global standards, SAE ensures consistent performance and safety across diverse electronic systems in vehicles and related transport technologies.
|
IPC Standards and Their Distinctiveness
IPC, previously known as the Institute of Printed Circuits and later as the Institute for Interconnecting and Packaging Electronic Circuits, is a globally recognized trade association. Established in 1957, its primary objective is to standardize the assembly and production requirements of electronic equipment and assemblies.
Over the years, IPC has evolved, reflecting the industry's growth from focusing solely on PCB assembly to encompassing packaging and electronic assemblies. Today, IPC stands with the tagline "Association Connecting Electronics Industries," emphasizing its pivotal role in bridging various facets of the electronics sector.
IPC standards are in the core of the electronics manufacturing industry, providing guidelines that ensure consistency, quality, and innovation. One of the most widely used standards, IPC-A-610, titled "Acceptability of Electronic Assemblies," sets the benchmark for electronic assembly quality worldwide.
This standard, along with others, is the result of collaborative efforts by industry volunteers from various regions, including China, the United States, and Denmark. IPC's standards cover a vast array of topics, from general terms and definitions (IPC-T-50) to specific design guidelines like IPC-2221, the Generic Standard on Printed Board Design. With over 3600 certified trainers globally, IPC's influence is undeniable, ensuring that electronic products meet the highest quality benchmarks.
IPC's standards are not just numerous but also comprehensive, addressing every conceivable aspect of electronics manufacturing. From the foundational principles of design to the intricate details of assembly, IPC's standards provide a roadmap for manufacturers to achieve excellence.
For instance, the IPC-6011 standard offers a generic performance specification for PCB assembly, ensuring that printed circuit boards meet rigorous quality and durability benchmarks.
Similarly, the IPC-4202 and IPC-4203 standards provide guidelines for flexible base dielectrics and adhesive-coated dielectric films, respectively, ensuring that even the materials used in electronics manufacturing are of the highest caliber. Such depth in standards ensures that every component, no matter how small or seemingly insignificant, meets a global benchmark of quality.
One of the standout features of IPC standards is their ability to evolve with the times. As the electronics industry undergoes rapid changes and technological advancements, IPC ensures that its standards remain relevant and up-to-date.
This adaptability is evident in standards like IPC-7351B, which provides guidelines for surface mount design and land pattern standards, reflecting the industry's shift towards miniaturization and high-density assemblies.
Furthermore, IPC's proactive approach in forming task groups in emerging electronics hubs like China and Denmark signifies its commitment to staying ahead of industry trends and ensuring that its standards are universally applicable, regardless of geographical or technological boundaries.
While there are numerous certifications and standards available in the electronics manufacturing industry, IPC stands out due to its comprehensive approach and global recognition. Here are some distinguishing factors:
- Global Acceptance: IPC certifications and standards are recognized and accepted worldwide, making them a preferred choice for manufacturers aiming for international markets.
- Industry-Specific Focus: Unlike generic certifications, IPC standards are tailored specifically for the electronics manufacturing industry, ensuring relevance and applicability.
- Continuous Evolution: IPC continuously updates its standards and certification programs to reflect the latest industry trends, technologies, and best practices.
- Collaborative Approach: IPC involves industry experts, manufacturers, and stakeholders in the process of developing and refining standards, ensuring that they address real-world challenges and needs.
EPTAC'S Role in Promoting IPC Standards
EPTAC stands as a beacon for professionals aiming to master IPC standards. Recognized as a leading provider of solder training and IPC certification programs, EPTAC has dedicated itself to ensuring that electronics professionals are well-equipped to implement IPC standards in their manufacturing processes.
With a team of experienced instructors and a comprehensive curriculum, EPTAC offers training sessions that delve deep into the nuances of IPC standards. These sessions not only provide theoretical knowledge but also practical insights, ensuring that participants can apply these standards effectively in real-world scenarios.
Furthermore, EPTAC's commitment to continuous learning and its emphasis on hands-on training make it an indispensable partner for those aiming to achieve excellence in electronics manufacturing through IPC standards.
Through its efforts, EPTAC bridges the gap between IPC's global standards and their practical implementation, fostering a culture of quality and consistency in the electronics industry.
About EPTAC
EPTAC is an internationally recognized leader in solder training and IPC certification, providing professionals with the skills to accelerate their careers, and businesses, the talent to succeed. For over 35 years, EPTAC has been helping corporations increase quality standards, improve productivity, and maximize profits. With 24 locations in North America, EPTAC continues to expand its offerings and exceptional instructional staff to provide easy access to knowledge and skill-based programs when and where the industry demands it. Access our scheduled programs through our website or schedule your own corporate on-site training. For information, call 800.643.7822 or contact us.