In an era marked by exceptional technological growth, the Consumer Electronics market has become a behemoth, boasting revenues amounting to an impressive US$1,028.00 billion in 2023 (Statista, Consumer Electronics – Worldwide). To maintain this momentum and to satisfy the annual growth projection of 2.32% (CAGR 2023-2028), ensuring the highest standards of quality in electronic manufacturing is of utmost importance. It becomes even more critical when considering that the largest segment, Telephony, has a market volume of US$498.30 billion in 2023, reflecting the immense financial and customer satisfaction implications of even the smallest defect. A critical stage in the manufacturing process of these devices is the 'bare board inspection.' This inspection serves to ascertain that the printed circuit board (PCB) - the foundational component upon which all parts of an electronic device will be assembled - is free of any flaws that might compromise the final product. With the Consumer Electronics market volume expected to reach a staggering 8,974.00 million pieces by 2028, and with an average of 1.08 pieces per person expected in 2023, bare board inspection plays an instrumental role in maintaining the stringent quality standards that are necessary in today's electronic manufacturing sector. This article delves into the intricacies of bare board inspection, spotlighting its pivotal role and the significant impact it has on quality assurance in electronic manufacturing.
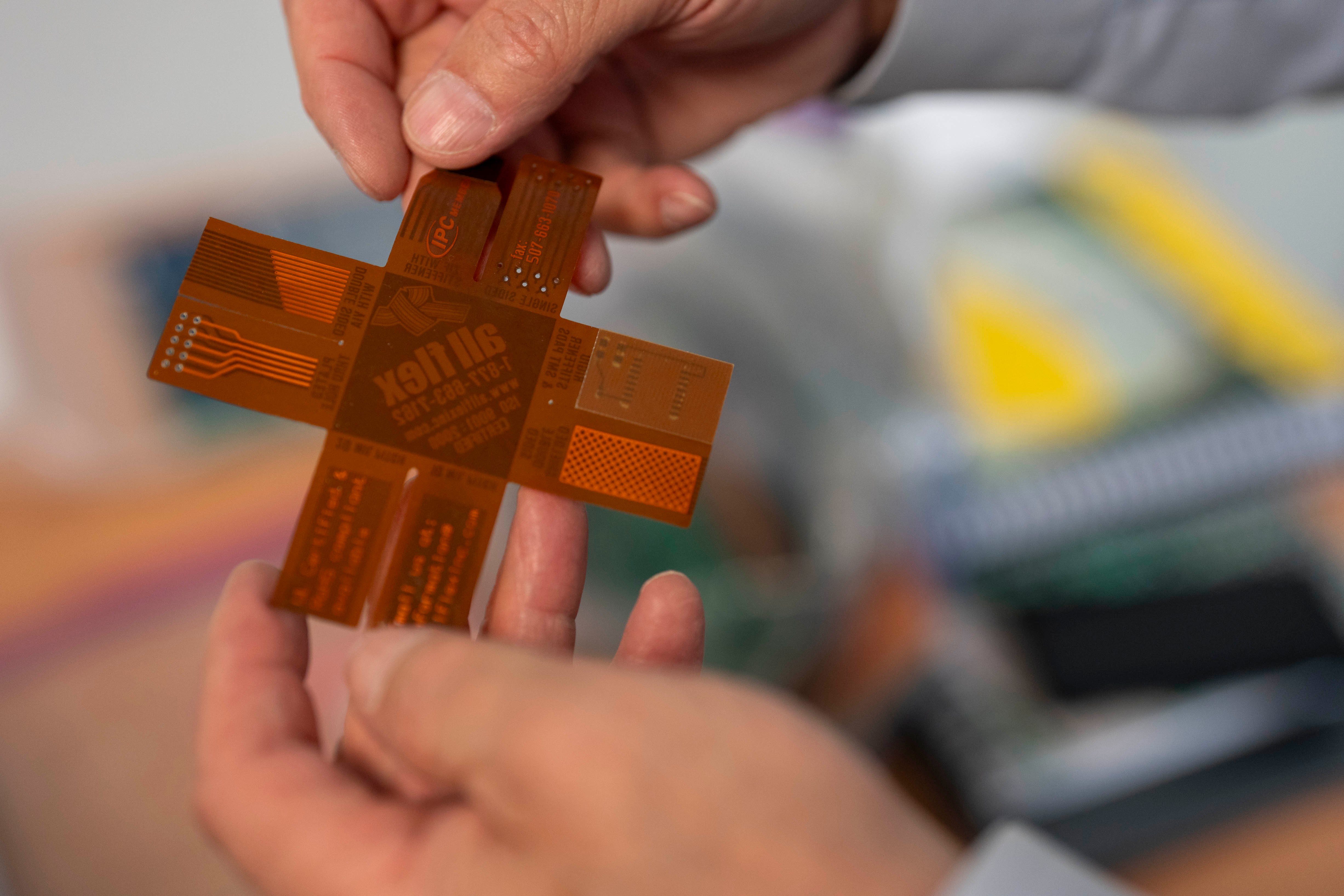
What is Bare Board Inspection?
Bare Board Inspection, often referred to as PCB (Printed Circuit Board) Inspection, is a quality assurance process that aims to identify defects or inconsistencies in the bare printed circuit boards before any electronic components are attached. This inspection forms an essential part of the electronic manufacturing process, as it is much easier, cost-effective, and less time-consuming to rectify defects at this stage rather than later in the manufacturing cycle when the board has been fully populated with components.
At its most fundamental level, the bare board inspection process can be carried out manually. This involves a visual check of the PCB by trained inspectors who look for overt defects such as incorrect hole sizes, misaligned traces, or physical damage. Despite the rise of automation, manual inspection still holds value in certain contexts, such as for smaller production runs, prototyping, or when a high level of expertise and judgment is required. However, it is labor-intensive, time-consuming, and susceptible to human error, particularly for complex, miniaturized designs common in today's electronics.
Automated Optical Inspection (AOI) is one of the most widely used methods for bare board inspection. AOI systems use high-resolution cameras to capture images of the PCB, which are then compared against a digital blueprint of the board using computer algorithms. The system checks for a variety of potential defects including shorts, opens, missing or extraneous metal, and more. AOI is highly efficient and capable of detecting even very small defects, but it is limited to inspecting the surface of the PCB and cannot detect issues within the layers of the board.
To inspect the internal structure of a PCB, particularly multilayer boards, Automated X-Ray Inspection (AXI) is employed. This technique uses X-rays to create an image of the board, allowing for the detection of defects such as shorts, opens, or voids in the internal layers that cannot be seen in an AOI inspection. While AXI is a powerful tool for inspecting complex, high-density boards, it is also more expensive and requires more time than AOI and is typically reserved for boards where internal defects are a particular concern.
With the advancement of technology, new inspection methods are being developed. For example, some manufacturers use infrared cameras to check for hotspots on a PCB, which can indicate potential issues. Others are exploring the use of AI and machine learning to improve the speed and accuracy of defect detection and to predict potential failure points based on the inspection data.
Why Bare Board Inspection is Necessary?
Ensuring quality in the realm of electronic manufacturing is pivotal, and this journey starts right from the foundation - the bare printed circuit board (PCB). Bare board inspection plays an indispensable role in this process. Neglecting this critical step in the production process could lead to catastrophic effects, severely undermining the device's functionality and reliability, and potentially leading to substantial financial and reputational damages.
A PCB is essentially the backbone of any electronic device. It provides the critical connection pathways for all the electronic components that will eventually be mounted on it. Therefore, even the slightest defect on a PCB, be it a tiny scratch, an incorrectly drilled hole, or a small misalignment of copper, can lead to the device malfunctioning. With the increasing miniaturization and complexity of modern electronic devices, the scope for errors and their potential impacts have only amplified.
If defects are not detected and rectified at the bare board inspection stage, they can lead to a series of problems later in the manufacturing process. First and foremost, defects can cause the electronic device to fail outright, leading to waste of resources and materials as the entire board must be discarded. Even more concerning are the intermittent failures, which can be more difficult to diagnose and may not manifest until the product has reached the end user, potentially leading to customer dissatisfaction and damage to the manufacturer's reputation.
Additionally, it is far more cost-effective to identify and rectify PCB defects during the bare board inspection than at later stages of production. Once components have been mounted onto the PCB, diagnosing and fixing problems becomes much more complex and time-consuming. For instance, a faulty PCB that has already been populated with components could require a complete rework, involving the removal and reinstallation of components, or even the scrapping of the entire board.
Bare Board Inspection in the Broader Context of PCB Manufacturing and Quality Control
Bare board inspection, while an essential quality control measure in its own right, does not function in isolation. Rather, it is intricately interwoven into the broader fabric of PCB manufacturing and overall quality control, acting as a key line of defense against potential flaws that could compromise the functionality of the final product.
The journey of a PCB starts with the design phase, where the blueprint for the circuit board is created. Following this, the manufacturing process kicks off with the creation of the bare board, which includes etching the copper pathways and drilling the holes for component placement. After the bare board has been produced, it's at this point that bare board inspection steps into the limelight. It serves as the final checkpoint before the PCB moves into the assembly process, where various components are soldered onto the board.
Each stage in this process - from design to assembly - comes with its own potential pitfalls and challenges. Mistakes in the design phase, for instance, can lead to a board that's fundamentally flawed. Manufacturing errors can create physical defects that could result in an unstable or unusable product. Bare board inspection serves as the critical interstice between these stages, ensuring that any issues are identified and resolved before they can cause problems down the line.
After the bare board inspection and ensuing assembly, the populated boards are typically subjected to further quality control measures, such as in-circuit testing and functional testing. These tests verify that the device functions as intended and meets all specified requirements. However, these later-stage quality controls are substantially more efficient when they're dealing with a board that's already been validated at the bare board stage.
In essence, bare board inspection forms a critical cornerstone of the broader quality control framework, facilitating smoother operations in subsequent stages. By identifying and rectifying issues at the foundational level, it significantly reduces the chances of defects propelling forward into later stages of production, thereby boosting the overall efficiency of the manufacturing process and enhancing the quality and reliability of the final product. Bare board inspection, therefore, not only ensures the integrity of individual PCBs, but also contributes significantly to the overarching quality control objectives of electronic manufacturing.
The journey to mastering quality standards in electronic manufacturing, particularly the IPC 620 certification, is a continuous process of learning, application, and improvement. With the right mindset, resources, and training partner, this journey can lead to significant benefits in terms of product quality, customer satisfaction, and business success. As we continue to rely more on electronic devices in our everyday lives, the importance of these quality standards will only continue to grow.
So, whether you are a professional seeking to advance your career or a business striving to improve your product quality and market competitiveness, mastering the IPC 620 certification is a step in the right direction. And with EPTAC's comprehensive programs and experienced instructors, you are in good hands on your journey to achieving and maintaining this prestigious certification.
Challenges and Future Prospects of Bare Board Inspection
The process of bare board inspection, while essential, is not without its difficulties. As electronic devices continue to evolve, becoming smaller and more complex, maintaining accuracy in the inspection process presents a significant challenge. The increased density of tracks and pads in modern PCBs make it harder to spot defects. Minute irregularities, which could have a substantial impact on the final product's functionality, might be missed by even the most sophisticated inspection systems.
Moreover, the requirement for advanced inspection equipment is another hurdle. High-resolution imaging equipment, X-ray machines, and specialized software are often necessary for reliable bare board inspection. Such technologies can be expensive to acquire and maintain, which can be a barrier for smaller manufacturers. Additionally, the effective use of this equipment requires specialized skills, adding to the demand for highly trained personnel.
Furthermore, the speed of inspection is an ongoing issue. With consumer electronics market growing rapidly and customer demand for faster production cycles, the pressure on manufacturers to speed up the inspection process is increasing. However, faster inspection can potentially compromise on the quality, leading to missed defects. Balancing speed and accuracy is, therefore, a persistent challenge.
Despite these challenges, the future of bare board inspection looks promising, with technology playing a key role in advancing the field. Emerging technologies such as Artificial Intelligence (AI) and Machine Learning (ML) hold significant potential for improving both the speed and accuracy of bare board inspection.
AI can be used to automate the inspection process, reducing the time taken and the potential for human error. Machine learning algorithms can be trained on vast amounts of data, allowing them to recognize and flag defects with a high degree of accuracy. Furthermore, they can adapt and improve over time, learning from each inspection to become more efficient and effective.
Similarly, advances in imaging technology are expected to further enhance inspection capabilities. For instance, the use of 3D imaging techniques can provide a more detailed view of PCBs, allowing for more thorough inspections, particularly for multi-layered boards.
Internet of Things (IoT) technology can also play a role in bare board inspection. IoT can be used to create a more integrated and efficient manufacturing process, where data from the inspection process is shared in real time across the production line. This could lead to faster response times when defects are detected, enhancing overall manufacturing efficiency.
Training and Certification Programs for Bare Board Inspection
As the complexity and precision requirements in bare board inspection increase, the need for skilled inspectors with a deep understanding of the nuances of the process becomes paramount. Training and certification programs play a critical role in maintaining high standards of quality and consistency in bare board inspection. These programs equip inspectors with the knowledge and skills needed to effectively identify defects and ensure that each PCB meets the required standards.
One of the leading organizations providing such training is EPTAC, which offers a comprehensive range of programs that cover all aspects of bare board inspection.
EPTAC offers six distinct certification programs covering bare board inspection:
- IPC-A-600 Instructor: This is a 3-day course that covers the IPC-A-600 specification in its entirety. The program utilizes visual examples to provide clear accept/reject criteria for all three classes of bare board fabrication and inspection.
- IPC-A-600 Specialist: Similar to the Instructor program, this course also focuses on the IPC-A-600 specification. However, it is targeted at specialists who need to apply the specification's standards in their roles.
- IPC-6012 Instructor: A 4-day course that helps develop a comprehensive understanding of the design, specifications, fabrication, and inspection of rigid printed boards (PCBs). The course relies heavily on the IPC-6012 and IPC-A-600 documents.
- IPC-6012 Specialist: This is another 4-day program aimed at operators. It offers an in-depth understanding of the design, fabrication, and inspection requirements of rigid printed boards, based on the IPC-6012 and IPC-A-600 standards.
- IPC-A-600 Standard Expert: This program is designed for individuals who wish to become subject matter experts on the IPC-A-600 standard. The 3-day course covers the IPC-A-600 specification and provides the opportunity to support the organization as a key subject expert on the standard.
- IPC-6012 Standard Expert: A 4-day course focusing on the IPC-6012 specification, this program aims to develop subject matter experts on the qualifications, performance requirements, and design, fabrication, and inspection requirements of rigid printed boards.
In addition to these six certification programs, EPTAC also offers four recertification programs, ensuring that certified inspectors stay up-to-date with the latest standards and practices in bare board inspection. Each of these programs aims to empower inspectors with the knowledge and skills necessary to maintain the highest standards of quality in electronic manufacturing.
By investing in such training and certification, manufacturers can ensure that their bare board inspection processes meet the stringent requirements of today's electronic devices, paving the way for superior product quality and reliability.
About EPTAC
EPTAC is an internationally recognized leader in solder training and IPC certification, providing professionals with the skills to accelerate their careers, and businesses, the talent to succeed. For over 35 years, EPTAC has been helping corporations increase quality standards, improve productivity, and maximize profits. With 24 locations in North America, EPTAC continues to expand its offerings and exceptional instructional staff to provide easy access to knowledge and skill-based programs when and where the industry demands it. Access our scheduled programs through our website or schedule your own corporate on-site training. For information, call 800.643.7822 or contact us.